Pulvérisateur - PWM ou sélection automatique de buses : quelle solution pour moduler la vitesse ou la dose ?
Deux technologies s’offrent à l’agriculteur qui souhaite allonger la plage de vitesse de travail de son pulvérisateur ou moduler la dose épandue, sans impacter la qualité d’application. Après les porte-buses à sélection automatique, la technologie PWM des buses à pulsation fait de plus en plus d’adeptes.
Deux technologies s’offrent à l’agriculteur qui souhaite allonger la plage de vitesse de travail de son pulvérisateur ou moduler la dose épandue, sans impacter la qualité d’application. Après les porte-buses à sélection automatique, la technologie PWM des buses à pulsation fait de plus en plus d’adeptes.
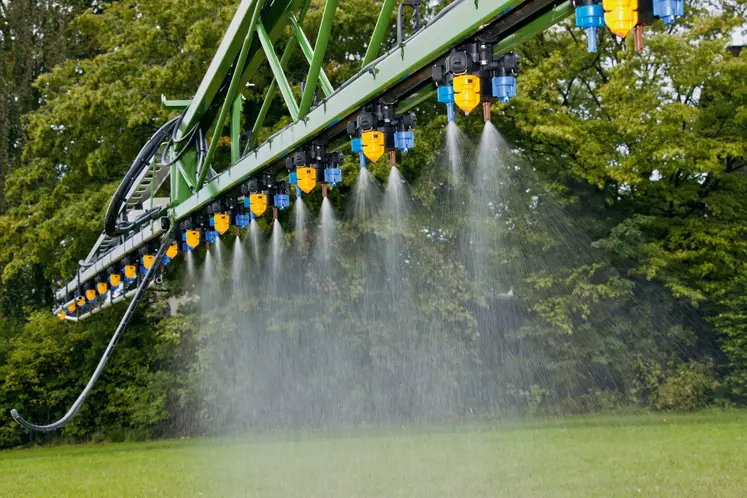
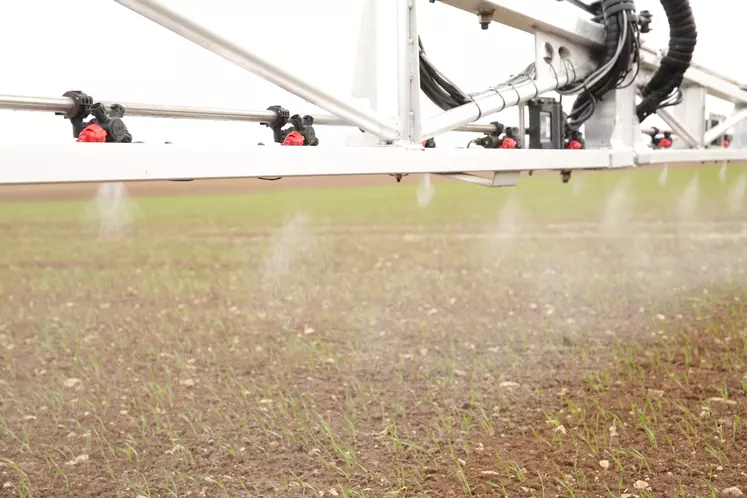
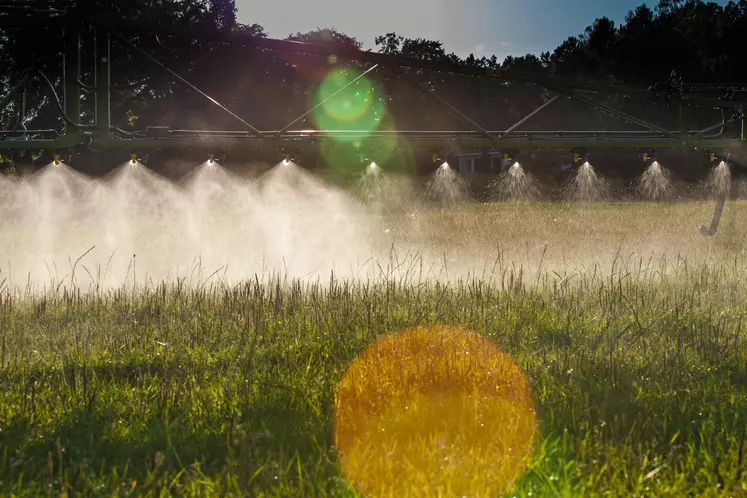

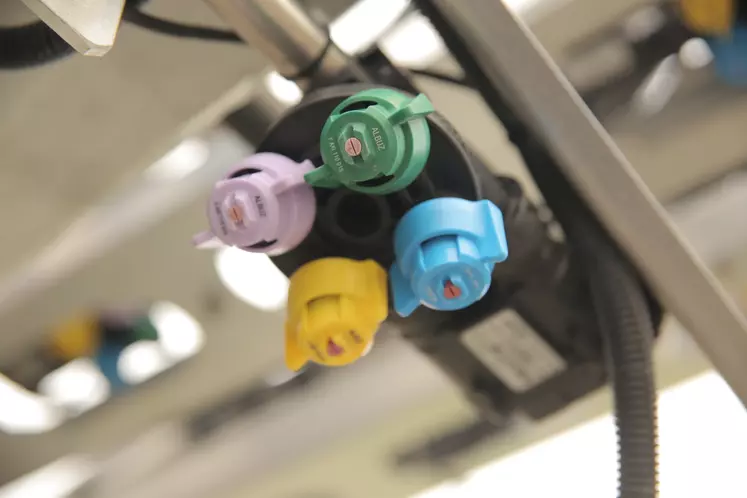
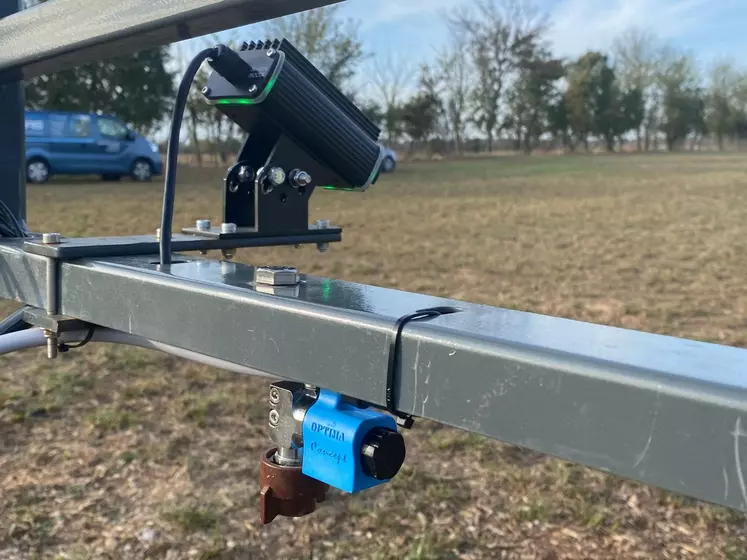

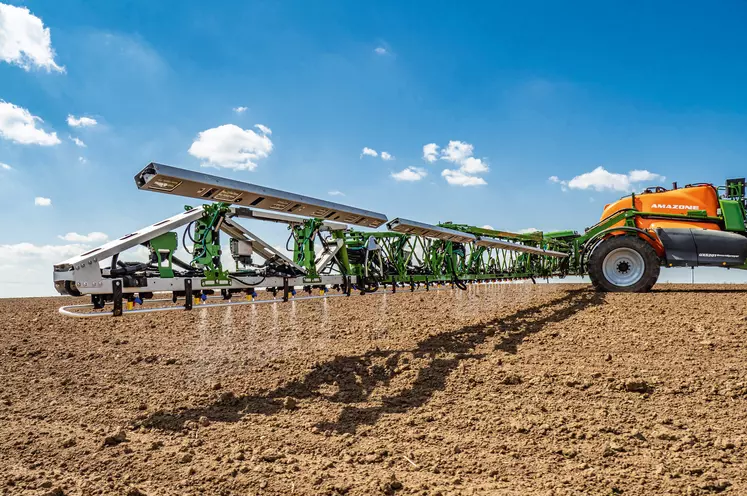
Afin de respecter la plage de pression optimale de fonctionnement des buses de leur pulvérisateur, les agriculteurs ont tout intérêt à investir dans un dispositif leur offrant plus de latitude dans les variations de vitesse d’avancement. Suivant la configuration des parcelles, il est en effet bien souvent difficile de maintenir une vitesse de travail constante. L’autre enjeu, pour les utilisateurs pratiquant la modulation de dose, est de pouvoir faire varier suffisamment le volume par hectare, sans dégrader la qualité de pulvérisation.
La première voie employée par les constructeurs européens depuis une dizaine d’années consiste à utiliser des porte-buses à sélection automatique. L’utilisateur définit une plage de pression pour chaque buse qu’il souhaite utiliser et le système sélectionne automatiquement la ou les buses les mieux adaptées en fonction de la vitesse d’avancement et de la dose fixée. Qu’ils soient à pilotage pneumatique ou électrique, ces dispositifs ont l’avantage d’être largement éprouvés, avec un fonctionnement garanti, quel que soit le type de buse employé et les conditions d’utilisation. Les dispositifs à quatre buses offrent de grandes plages de variation de débit, permettant par exemple d’évoluer de 8 à 20 km/h, ou encore de moduler la dose d’azote liquide de 70 à plus de 200 litres par hectare. Le multibuse impose toutefois d’être vigilant sur la fluctuation de la pression, qui peut impacter la taille des gouttes, notamment avec des buses standards, les buses antidérive à injection d’air étant moins sensibles aux changements de pression.
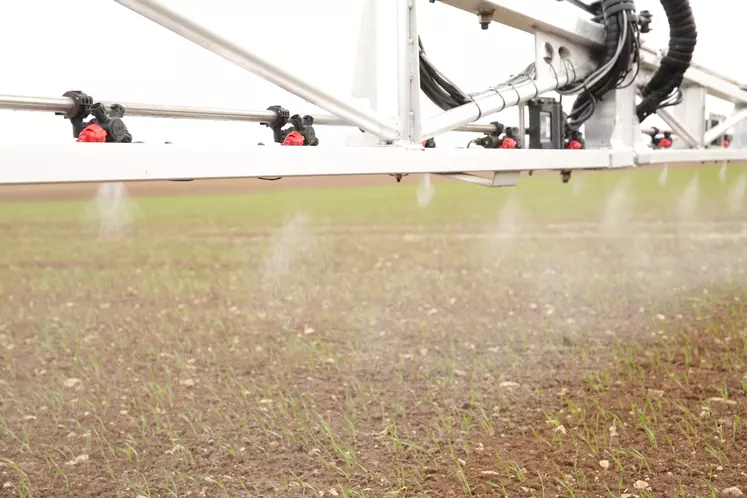
Attention aux phases transitoires avec le multibuse
« Pour rester dans la plage optimale de la buse, il ne faut pas faire varier la pression de plus de 1,5 à 2 bars, ce qui correspond à une variation de vitesse de 3 à 4 km/h », rappelle François-Xavier Janin, chef produit chez France Pulvé. Le passage d’une buse à une autre, voire à deux buses simultanées, engendre des phases transitoires avec des changements de pression, qui peuvent sursolliciter la régulation du pulvé. « Il est essentiel de connaître à quels niveaux de vitesse d’avancement se situent ces phases de transition où le dispositif va hésiter entre deux buses et provoquer une régulation de pression en dents-de-scie. L’agriculteur doit ainsi éviter le plus possible de rester dans ces zones de vitesse », explique Emmanuel Lévêque, chef produit chez Amazone.
Le multibuse s’accompagne d’une mise en œuvre de la modulation par tronçons, ce qui est généralement suffisant, compte tenu de la résolution des cartes de préconisation. La plupart des constructeurs proposent également une coupure par tronçons, la coupure à la buse étant généralement disponible en option, sauf pour certains qui le montent de série, comme Amazone. « Le fait de moduler par tronçons limite l’efficacité des dispositifs de compensation de courbe qui évitent le surdosage à l’intérieur du virage et le sous-dosage à l’extérieur, avertit Benjamin Desindes, chef produit chez Kuhn. La technologie des buses PWM s’impose pour avoir une vraie modulation progressive sur toute la largeur de rampe. »
Les buses PWM travaillent à pression constante
Cette seconde solution, apparue plus récemment en Europe, nous vient des Etats-Unis où elle fait ses preuves depuis une vingtaine d’années. Elle se caractérise par l’utilisation de buses à pulsation utilisant la technologie PWM (Pulse Width Modulation, pour modulation de largeur d’impulsion). Le principe est de faire varier le débit en modulant la durée du cycle d’ouverture des buses. Il est alors possible de modifier la vitesse de travail ou le volume/hectare en conservant la même buse à pression optimale d’utilisation. « Contrairement au multibuse qui impose des changements de pression avec des phases de transition, le PWM permet de travailler à pression constante, garantissant une stabilité de la taille des gouttes et de la dérive », argumente Benjamin Desindes. En guise d’illustration, Emmanuel Lévêque compare la sélection automatique de buse à une transmission powershift, qui impose des changements de rapports et des variations de régime, tandis que les buses PWM s’apparentent à une variation continue, qui permet de faire varier la vitesse en continu, indépendamment du régime moteur. Outre le fait d’offrir la coupure et la modulation buse à buse, ce système a l’avantage de limiter le nombre de jeux de buses à utiliser.

Une seule buse, dont on régule le temps d’ouverture
Techniquement, la technologie PWM repose sur l’utilisation d’un solénoïde monté sur chaque porte-buse, qui en contrôle l’ouverture et la fermeture selon une fréquence stabilisée. En fonction des systèmes utilisés, cette fréquence varie de 20 à 50 hertz selon les constructeurs. Plus simplement, la buse s’ouvre et se ferme de 20 à 50 fois par seconde. La modulation de débit s’effectue en faisant varier la durée d’ouverture au sein d’un cycle d’ouverture/fermeture. Le fonctionnement est transparent pour l’utilisateur qui a simplement à sélectionner la buse utilisée, la taille de goutte et le volume/hectare. Cas particulier, la technologie PWFM, développée par Agrotop et utilisée par Amazone, permet de faire varier non seulement la durée d’ouverture, mais aussi la fréquence d’impulsion.
Selon la fréquence appliquée, les buses PWM permettent de multiplier par deux ou par trois la plage de vitesse d’une buse. « On atteint facilement une amplitude de 10 à 12 km/h, sans risque de phénomène de hachage », assure François-Xavier Janin, tout en reconnaissant que le PWM impose un bon respect de la hauteur de rampe pour garantir le recouvrement. « Il faut aussi veiller à ne pas maintenir une vitesse d’avancement qui correspond à la phase de transition entre la pleine ouverture des buses et l’activation du hachage », note le spécialiste.
Le PWM n’est pas compatible avec toutes les buses antidérive
Le fonctionnement plus pointu de la technologie PWM a aussi ses contraintes. En termes de confort d’utilisation, contrairement au multibuse, il ne permet pas un changement de buse sans descendre de la cabine, à l’exception de la solution ExactApply de John Deere qui combine la sélection de buses et le PWM. Mais c’est surtout sur le choix des buses que le PWM peut devenir limitant. En effet, si les modèles classiques ne posent aucun problème, les buses antidérive à injection d’air ne sont pas toutes compatibles avec le PWM. « Certaines buses à injection d’air homologuées pour l’antidérive ont trop d’inertie pour supporter une alimentation en pointillé, confirme Emmanuel Lévêque. En Allemagne, un protocole spécifique de réhomologation des buses antidérive est mis en œuvre spécifiquement pour le PWM. » Les fournisseurs de buses travaillent sur la question et l’offre en buses antidérive compatibles PWM va rapidement s’étoffer. « Des tests mis en œuvre en collaboration avec l’Inrae nous ont déjà permis de confirmer que plusieurs buses à injection d’air chez Teejet et Albuz se comportent très bien avec le PWM, y compris avec une fermeture à 50 % », rassure François-Xavier Janin. Les premiers utilisateurs ont également observé certaines limites pour épandre de gros volumes en azote liquide. Mais le problème a été résolu avec les nouvelles générations de porte-buses et d’électrovannes qui ont de plus grosses sections de passage. »
Autre précaution à respecter avec la technologie PWM, les risques de bouchage étant plus importants, il est indispensable de ne pas négliger les phases de rinçage. « Dans le cas des mélanges, il faut veiller à avoir une bouillie homogène et il est nécessaire de contrôler plus souvent les filtres, précise Benjamin Desindes. Avec des produits visqueux et denses ou encore avec certains adjuvants, le risque d’usure n’est pas négligeable. » Le PWM utilise en effet de nombreuses pièces en mouvement. « On n’a pas encore suffisamment de recul sur leur durée de vie, mais celle-ci sera très dépendante des produits appliqués et des pratiques de l’utilisateur », avertit Emmanuel Lévêque.
La pulvérisation ciblée impose la technologie PWM
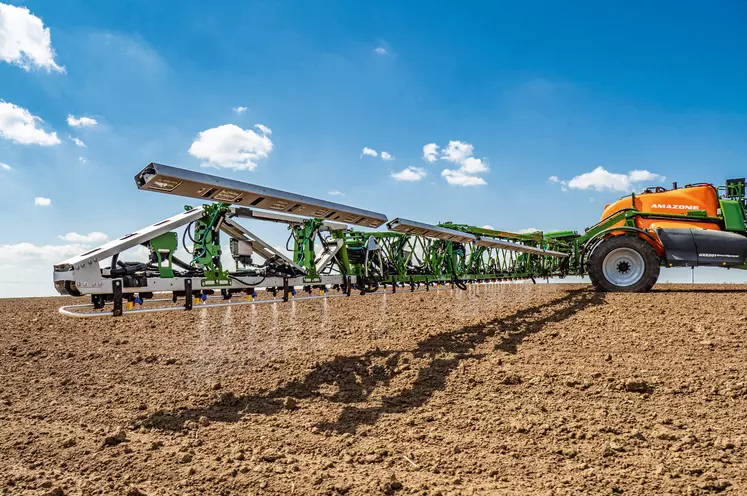
À budget équivalent, les buses à pulsation ont un argument qui semble imparable pour l’avenir, face à la sélection automatique de buse. La réactivité de la technologie PWM apparaît en effet comme un passage obligé pour accéder à la pulvérisation ultralocalisée. « Les buses PWM sont les seules à répondre aux exigences de la pulvérisation ciblée qui va s’imposer dans les prochaines années », estime Benjamin Desindes. Comme l’a fait John Deere avec son ExactApply, on pourrait même voir apparaître de nouvelles solutions associant la sélection de buse et le PWM.
La technologie PWM a aussi l’avantage d’être plus facilement adaptable sur un pulvérisateur existant. « Nous avons des demandes de rétrofit en spot spraying pour des appareils de 3-4 ans, sur lesquels nous sommes en mesure d’adapter à la fois le PWM et les caméras de détection de notre solution de pulvérisation ciblée Sniper », illustre François-Xavier Janin.
Un porte-jet PWM innovant
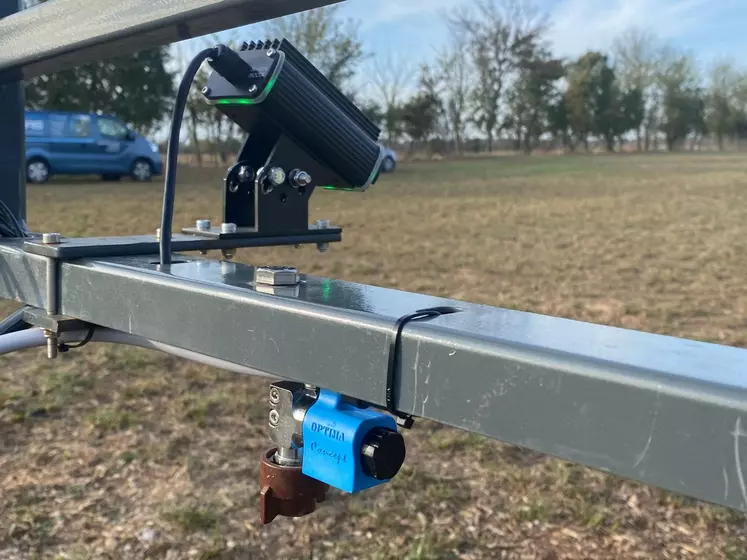
L’entreprise française Optima Concept a développé sa propre solution PWM appelée SRP avec un porte-jet caractérisé par son très faible volume mort. Cette particularité a l’avantage de rendre ce dispositif breveté beaucoup plus réactif que les solutions existantes sur le marché. « La conception de notre système SRP permet de réduire très nettement le temps de latence à l’ouverture et à la fermeture de la pulvérisation, grâce à notre circulation. On obtient instantanément la bonne taille de goutte qui est conservée avec des rapports cycliques allant de 95 à 10 %, quand de nombreux systèmes descendent difficilement en dessous de 50 % », argumente Luc Lahy, directeur commercial pour la société nordiste. Spécialiste de l’électronique embarquée, Optima Concept utilise un protocole Bus Can, de manière à simplifier l’architecture électronique et à obtenir un système très réactif, particulièrement adapté pour la pulvérisation ciblée. L’entreprise vient d’ailleurs de créer la marque XeBee en partenariat avec la société CarbonBee, de façon à proposer une solution complète de traitement ultralocalisé en première monte ou en rétrofit, combinant un terminal tactile et les porte-jets SRP d’Optima concept, associés à des caméras hyperspectrales fournies par CarbonBee, permettant de moduler les intrants en fonction des besoins de la culture et de pulvériser uniquement les adventices suivant le contexte (vert sur marron ou vert sur vert) avec la modulation en temps réel. « Cet équipement peut également être complété par des capteurs ultrasons pour un parfait suivi de rampe. »